How a Food Packaging Industry Giant Left Pen and Paper Behind to Streamline Their Workflows
A look behind the scenes at how Weidenhammer transformed their record-keeping from a burden into an asset.
Podcast
In this episode, two leaders in food packaging discuss their experience in converting to Provision for digital food safety and quality assurance.
Reid ThorpeQuality Control Manager, Weidenhammer |
Glenn EmoryGeneral Manager, Weidenhammer |
The Client
Weidenhammer is an American manufacturing operation that produces packaging and machinery for bulk ice cream.
Weidenhammer New Packaging was founded in Heidelberg, Germany in 1955. Innovative engineering has allowed them to emerge as market leader in foodservice manufacturing, where they command nearly 25% market share for bulk ice cream packaging. Weidenhammer formed a joint venture with Sonoco Products in 2014, and is now headquartered in Kansas City, where they operate one major manufacturing plant.
SectorFood Packaging |
Provision UsageThree Months |
Food Safety CertificationsTransitioning to FSSC 22000 |
Regulatory RegionKansas City |
The Challenge
A certification upgrade uncovers the constraints of analog records.
Weidenhammer kept records on paper and in Excel for their safety and quality procedures. Operators were strained to remember timing and rules pertinent to their procedures, and managers often lost time to repetitive reminders and review. This led to a great deal of hassle during audit prep. It was difficult to gauge ongoing opportunities for improvement, and changes were cumbersome when issues arose.
When they decided to upgrade Weidenhammer’s food safety certification to FSSC 22000, Glenn Emory, General Manager, and Reid Thorpe, Quality Control Manager, decided they needed to upgrade their systems as well. It was time to digitize and improve their documentation to open new opportunities for Weidenhammer’s growth.
The Breakthrough
Finding a comprehensive tool without oppressive pricing or daunting technical demands.
While Reid and Glenn recognized the need for digital food safety and quality data, they also recognized that many tools were not a fit. Food companies often struggle with technology that is geared to a large enterprise, which can be overcomplicated, rigid, and expensive when implemented in a small or mid-sized business.
![]()
“One of our owners is a $7 billion U.S. publicly traded company. We would’ve drowned in their systems.”
Glenn Emory • General Manager, Weidenhammer
Reid and Glenn needed a tool they could implement on the floor. It was critical for non-technical operators to provide clear data without extensive training. Weidenhammer also needed to minimize changes, keeping templates and procedures familiar – only enhanced. Reid and Glenn ultimately selected Provision for its usability and flexibility, which allowed easy customization to their documentation, and a fast learning curve for their teams.
![]()
“The UI design is really, really good because it eliminates the need to dig for things; it’s all very straightforward. We were unaware that software like this existed, and as soon as it came to our attention, I was sold almost immediately.”
Reid Thorpe • Quality Control Manager, Weidenhammer
The Transition
Leaning on customized services to nail software configuration and team training.
Weidenhammer chose Provision to have important data at their fingertips. But there were more possibilities in store than just banishing dusty binders. Provision’s flexible reminders, alerts, workflows, and reporting meant that Reid could streamline almost anything he had previously wrangled manually.
Weidenhammer utilized the implementation services from Provision to simplify their transition. Configuration was managed with concierge-like support. Reid shared his analog files and requests, and Provision created the digital templates with smart enhancements that met his specifications.
![]()
“As far as the simplicity of it, it’s literally like you took the Xerox hard copies we had, and they’re just fully digitized. Nothing is missing and everything is seamlessly integrated.”
Reid Thorpe • Quality Control Manager, Weidenhammer
Reid was particularly interested in improving Weidenhammer’s most complicated forms. Instead of operators reading lengthy instructions and handwriting answers, he wanted them to pick items from a clean drop-down menu, and have follow-up steps automatically hide or reveal. For example, if a line operator was doing a pre-op inspection and selected one machine, then only the questions pertinent to that machine would appear.
![]()
“The way that things can speak to and integrate with one another is phenomenal. All of the documentation, the SOPs, images – all of that can be linked.”
Reid Thorpe • Quality Control Manager, Weidenhammer
After their digital workspace was configured, Reid formed a project plan with Provision that divided the rollout into several phases. This phased approach prevented overwhelm for team training, and allowed Reid to continually apply learnings into each subsequent process. Reid started with production processes before adding in sanitation and maintenance. Provision has been introduced to Weidenhammer with iPads on the floor.
The Benefits
1.
Operator Guidance
Reid linked guidance documents such as SOPs directly into commonly-used forms, which proved an enormous boon. Employees could quickly view instructions relevant to a particular task, and were far less likely to guess at important procedures. Automatic rules flagged incomplete or incorrect data in records, allowing quick operator revisions in real-time. This not only reduced errors and improved efficiency, it also reduced tension between management and staff. Together, these improvements empowered Weidenhammer’s teams to feel a sense of ownership over their processes, which improved buy-in for food safety culture.
![]()
“Employees on the floor now have access to all of the things they need to know, rather than relying on semi-annual or annual training.”
Reid Thorpe • Quality Control Manager, Weidenhammer
2.
Timeliness
Reid used the task dashboard in Provision to clearly organize Weidenhammer’s record-keeping. This clarified individual and team responsibilities, deadlines, and even which templates to use for each activity. The automatic notifications and overdue tracking alleviated the team’s hectic feeling of scrambling.
![]()
“Having the ability to task my counterparts with a form in real time eliminates a mental struggle. Now instead of just having an email and then setting your own reminder on your phone, Provision already has that task for us and we can see if it’s overdue or not.”
Reid Thorpe • Quality Control Manager, Weidenhammer
3.
Agile Changes
Weidenhammer has earned a reputation for continuous improvement. Procedures are regularly reviewed to advance process control, and records are adjusted to capture the right data in the clearest fashion. However, these changes were painstaking on paper. Reid used Provision to achieve automatic versioning, which allowed him to instantly track a change log, block access to historic versions, and update documentation across all linked appearances. Teams were easily brought up-to-date.
![]()
“Whenever revisions were needed to be made, it would mean getting rid of all the old hard copies and scouring absolutely every inch of that Excel sheet before it was put out to the floor. Whereas now, the software is capable of changing on a whim if needed.”
Reid Thorpe • Quality Control Manager, Weidenhammer
4.
Audit Readiness
Reid used Provision to unify documentation that was previously scattered across paper, scanned files, and Excel spreadsheets. Using escalation workflows, any issues in records were managed in real-time. And submissions were automatically sorted by their status, folder, user, version, date, and more. This all simplified audit preparation. Reid could simply use reports to summarize and search Weidenhammer’s historic records, whether on-site or remote. It became faster for their teams to retrieve documentation and find outlying data.
![]()
“Instead of going into a local drive, trying to remember where we had stored a folder, and manually opening and closing a million PDFs to find what I was looking for – everything is immediately right there.
Reid Thorpe • Quality Control Manager, Weidenhammer
5.
Management Insight
By centralizing and structuring their data, Reid and Glenn gave Weidenhammer the ability to analyze and identify trends in quality and safety. Customizable reporting in Provision allows their teams to make informed decisions with up-to-the-minute information. Weidenhammer is now better prepared to capture opportunities for improvement.
![]()
“We’ve always had robust data collection, but we haven’t had data management. That’s one of the things we’re excited about with Provision – being able to take the pieces of data, which we used to have in disparate locations, putting those in one spot, and then being able to make decisions off our data.”
Glenn Emory • General Manager, Weidenhammer
The Results
From burdensome chore to valuable insights, Weidenhammer put their records to work for them.
Reid and Glenn have used Provision to make their teams more coordinated and informed. Records are seen as less of a burden, and more so as building blocks that contribute to data-driven decisions. Weidenhammer now has the flexibility to implement continuous improvements without straining their procedures or documentation.
![]()
“The flexibility and the ease of use are my favourite parts. Provision helps us look at our quality trends and any defects over time, instead of just going off of guesswork.”
Reid Thorpe • Quality Control Manager, Weidenhammer
Weidenhammer’s results don’t stand alone – a mass shift is happening as packaging companies embrace new tools for better insight. Baer & Associates is a major American packaging distributor; its President, Pat Loftus, expects to see more smart documentation as digitization accelerates among his clients and suppliers.
![]()
“Provision doesn’t just make packaging companies safer – it gives them the keys to better process control, often making their production more efficient and their products a higher quality.”
Pat Loftus • President, Baer & Associates
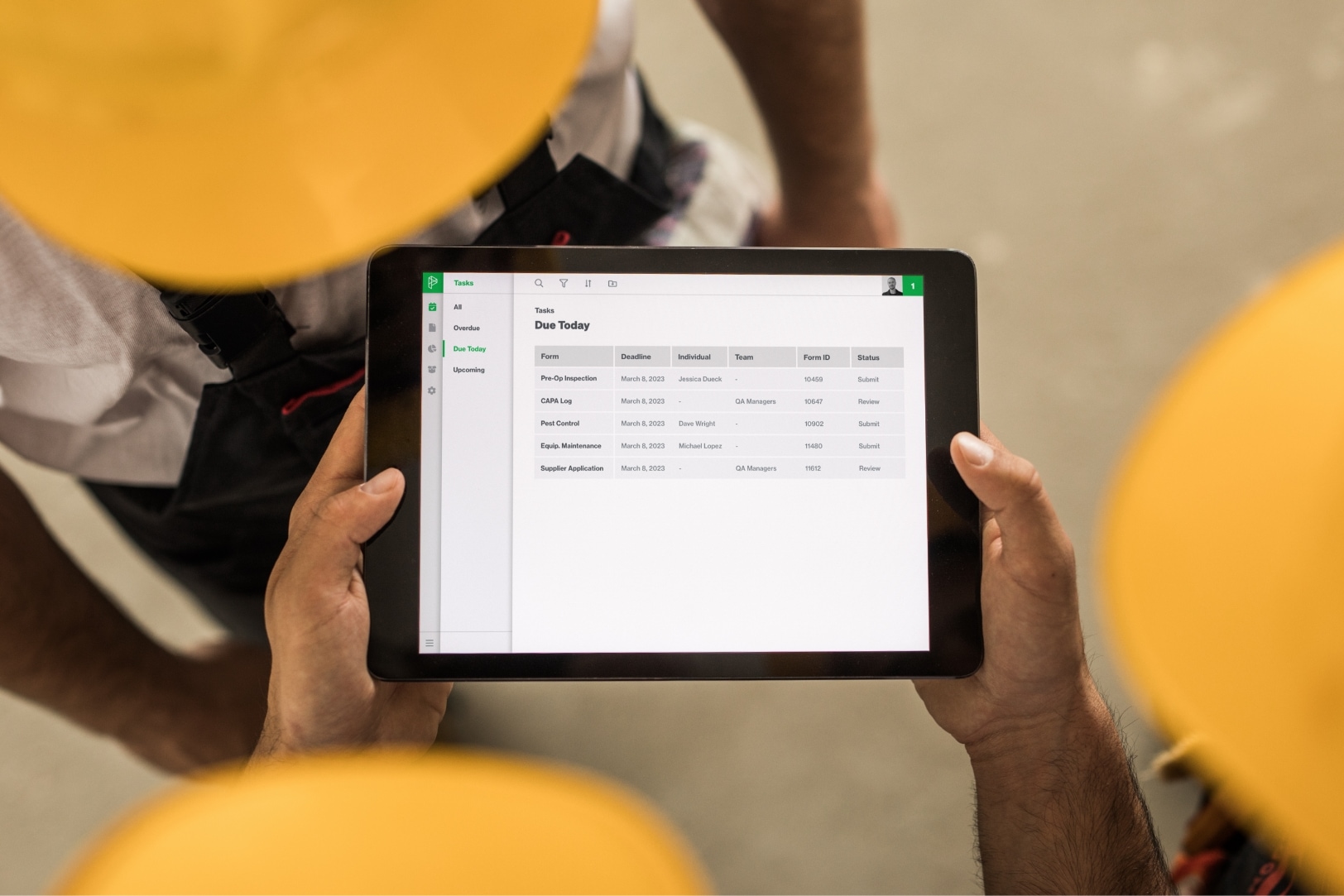
Time Savings
Estimated by Reid Thorpe, Quality Control Manager at Weidenhammer
10% |
Time saved on data entry |
40% |
Time saved on mock recalls |
50% |
Time saved on record review and verification |
75% |
Time saved on audit preparation |