Food safety managers are under more pressure than ever, juggling thousands of data points to maintain market access. Will packers invest in these unsung heroes as their compliance requirements escalate?
Compliance has always been a priority for fresh produce packers. But new requirements in traceability, sustainability, customer addenda, and labor laws are rapidly ballooning the documentation requirements. The challenge is becoming more apparent as packers face natural disasters, remote work, and increasingly unannounced audits.
While many operations have managed to stay compliant on paper, many managers feel like they're drowning in their duty to stay audit-ready. Do repetitive daily tasks bog down your operation, preventing you from managing the big picture in fresh produce quality and safety?
-
Chasing staff to complete records on time
-
Continually reminding staff of standard procedures
-
Constantly catching incomplete or deviant records
-
Driving site-to-site for document review
-
Binder-flipping to find data
In multi-location operations, this challenge intensifies. We ran the numbers—across 550 fresh produce clients, the median grower is 68 miles from their packer. With paper documentation, there are only two options: incur costly travel for on-site review, or hunt down issues in scanned images and discuss them by phone. This inefficiency is causing many packers to feel behind the eight ball in monitoring their networks. What can be done to solve the issue?
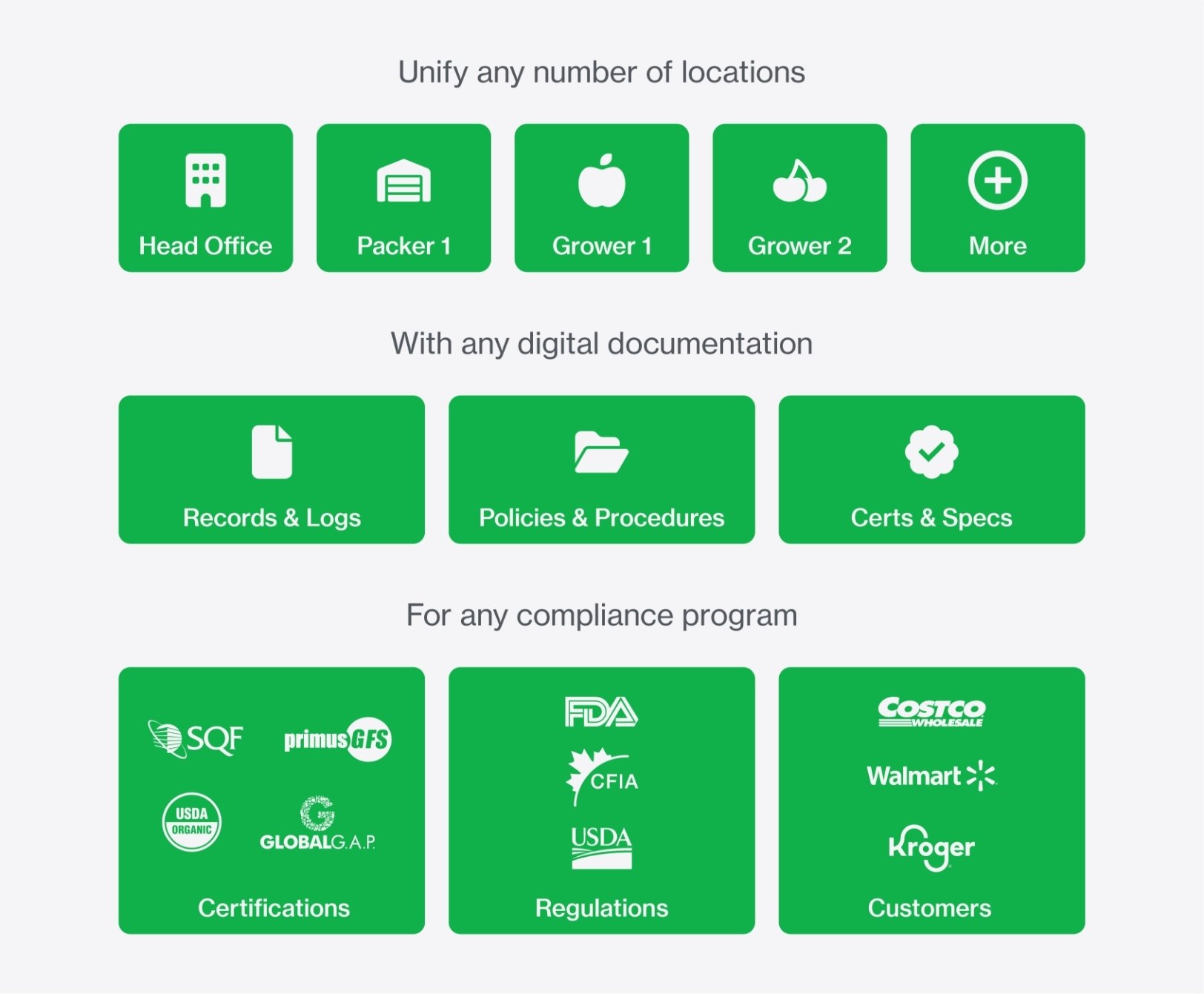
-
1.
Automate your reminders with task notifications to users or teams.
-
2.
Eliminate guesswork by displaying SOP guidance inside related records.
-
3.
Reduce ESL errors with live translation for 109 languages.
-
4.
Update versions for a network of documents in just one click.
-
5.
Prevent staff from submitting incomplete or non-compliant records.
-
1.
Learn of major deviations instantly with smart rules that trigger escalation alerts.
-
2.
Check who's overdue on which activities in one automatic summary.
-
3.
Track ongoing compliance metrics in customizable reports.
-
4.
Use dashboards to compare performance across packhouses and growers.
The Impact for Managers
Digital Efficiency is a Stepping Stone to Enhance Process Control
Managers can only be as effective as their resources allow. Using food safety software such as Provision, managers gain the time and the tools they need. With this advantage, packers are making data less of an organizational risk for audits, and more of a strategic asset for improvements in quality and safety.
-
Achieve up to 80% time savings in food safety management
-
Mitigate risks in achieving safety and quality compliance
-
Build management insight to enable continuous improvement
Since proving these outcomes, Provision has been adopted by fresh produce packers across the world, big and small.
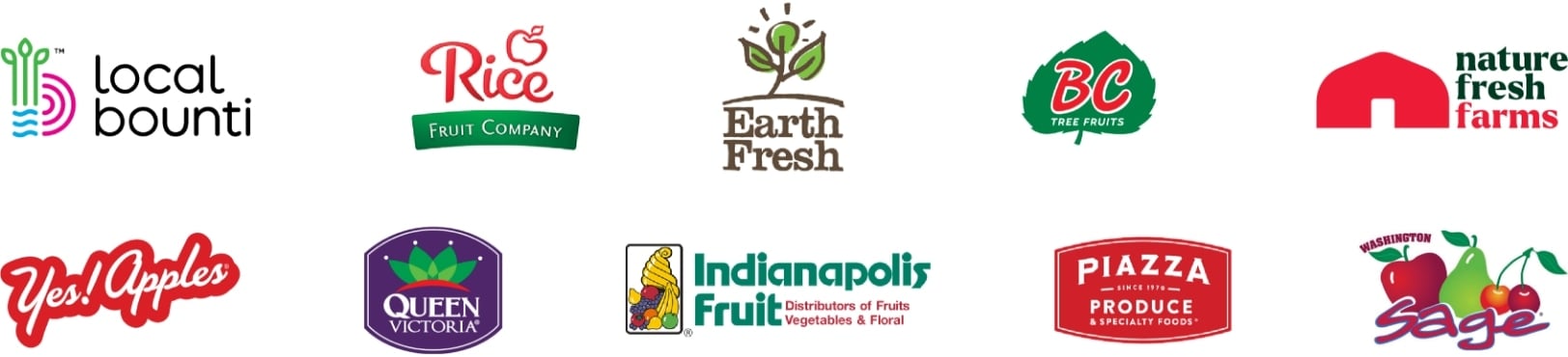