How Progressive Produce Prepared for PrimusGFS & Organic Audits 80% Faster
Arturo Coronado was fighting an uphill battle as he managed food safety binders across three facilities at Progressive Produce—until digital records doubled productivity.
The Client
Progressive Produce is a year-round grower, packer, shipper, and third party logistics provider of produce throughout North and South America.
Established in 1967, Progressive Produce has grown over the years to become a single source for globally-sourced fruit and vegetables, handling everything from potatoes and citrus to onions and asparagus. Their emphasis on innovation, sustainability, and quality has led them to be an industry leader that supplies major retailers.
Sector
Fresh Produce & 3PL
Headquarters
La Mirada, CA
Certifications
PrimusGFS, USDA Organic
Facility Size
190,000 square feet
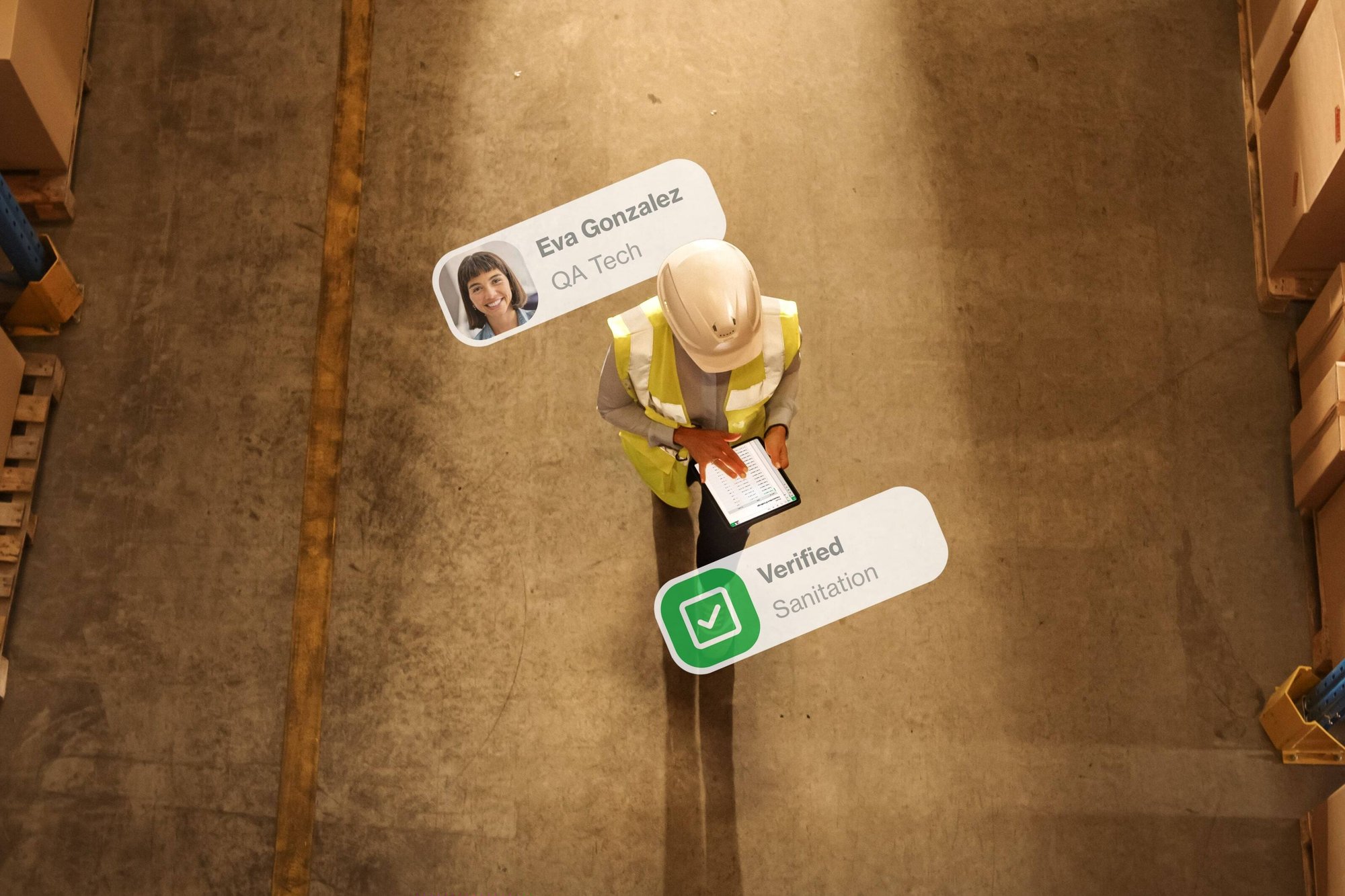
-
Three separate facilities with differing records left a mountain of paper to sort through before audits.
-
Static binders full of data hindered management analysis of trends and slowed decision-making.
-
Different versions of paperwork for English and Spanish inputs multiplied the amount of documentation to review and organize—and left room for miscommunication.
-
Stepwise Implementation
In order to focus attention onto successful adoption at each stage, the team at Progressive Produce began by digitizing a smaller number of forms, including Food Safety and Sanitation, before rolling out into other areas like Logistics, Shipping, and Safety.
-
Custom ConfigurationProgressive worked together with Provision's Client Success team to tailor their platform's configuration, setting management up for success from day one.
-
Minimized Change ManagementProvision's form building capability can digitally recreate existing forms, putting familiar tools into operators' hands for quick adoption and easy understanding.
-
1.
-
Live translation harmonizes English- and Spanish-speaking team members and improves communication
-
Centralized documentation empowers food safety culture through real-time collaboration between managers and operators
-
Embedded SOP guidance ensures understanding for staff
-
2.
-
Smart rules and team workflows allow management to review and verify quickly—identifying problems faster for quick corrective actions
-
Forms can be constructed with built-in calculations for a variety of metrics, including counting deviations noted, tabulating chemical formulations, and more—taking the guesswork out of monitoring
-
Customizable reports allow managers at Progressive to see the trends they need while filtering live by site, employee, equipment, and more
-
3.
-
Searchable records makes finding past data a snap both prior to and during an audit
-
Linking forms together in automated sequences streamlines navigation through records
-
Easy task assignment and follow-up, including tracking for missed tasks and late records, mean that missing input isn't found the week before an audit—it's seen as soon as it's overdue
Steps in the Right Direction
Having cut the time spent on their food safety documentation in half, Progressive Produce is already looking for new opportunities to streamline their departments with Provision.
With strong results and a positive reception for their new digital documentation tools in the food safety department at Progressive, there are already plans in place to expand usage into health and safety. The visibility and oversight allowed by bringing on Provision has opened the door for a new wave of success and growth powered by better root cause analysis, verification, and continuous improvement.
-
25%Time saved on data entry
-
40%Time saved on team management
-
80%Time saved on record review and verification
-
80%Time saved on audit preparation