Global food safety schemes benchmarked to GFSI frameworks - and the retailers that follow them - now evaluate how companies manage and share data. The December 2024 Benchmarking Requirements introduce new clauses on "expanded data management & transparency," a clear signal that reliable digital records are moving from competitive advantage to baseline expectation.
Yet raw inspection logs don't magically become insight. Only complete, trustworthy, and aggregated data reveal patterns - recurring hot spots, sanitizer dips after changeovers, that one cooler that drifts on long weekends. These trends guide preventive actions far better than any one-off fix.
Equally important, however, is that humans remain indispensable. Software can watch every sensor and crunch every data point, but people supply context, judgment, and decisive action. The safest operations let automation keep relentless watch while skilled teams focus on solving the right problems.
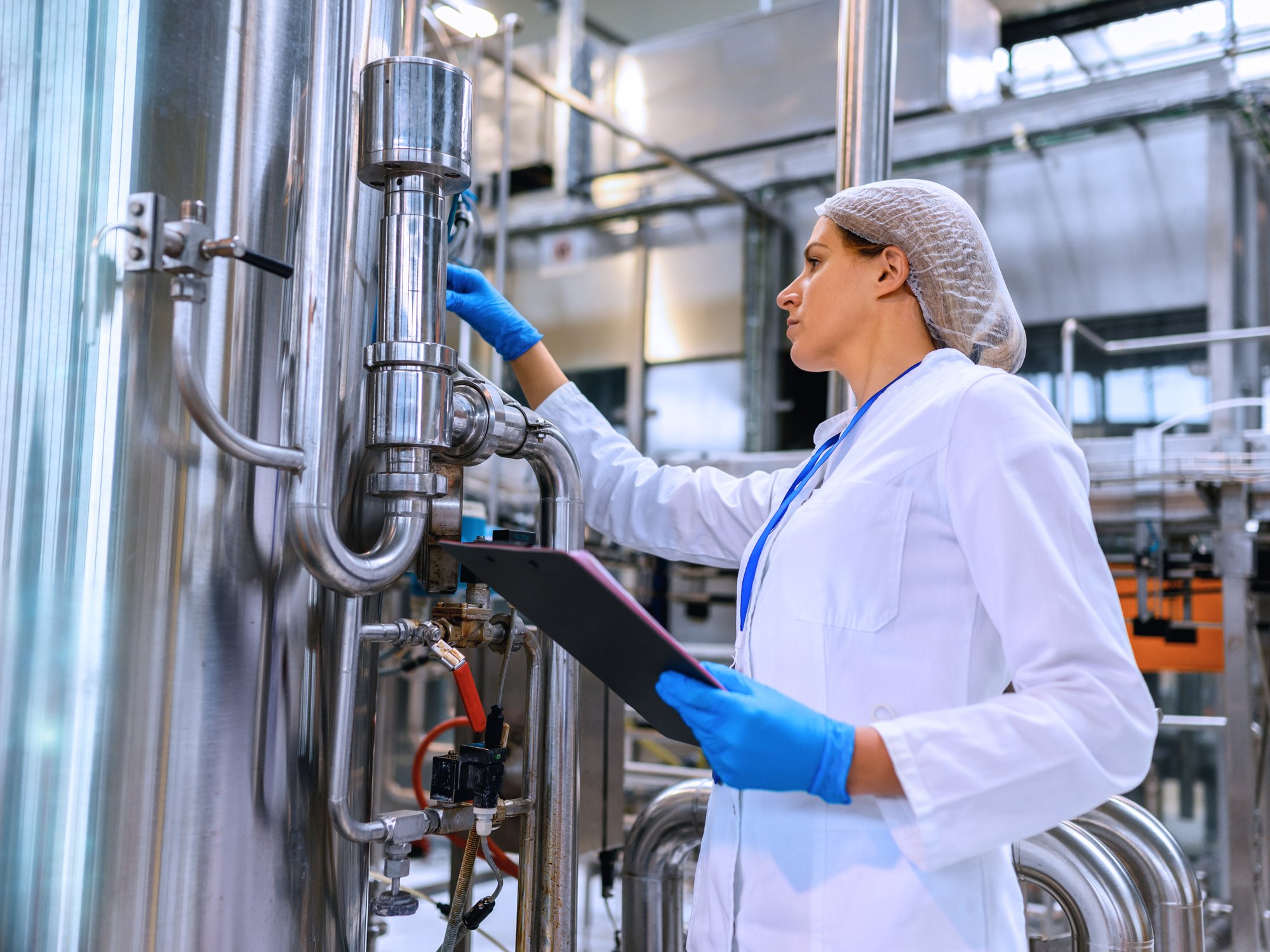
Digital tools shoulder the repetitive monitoring work and surface problems the moment they occur, giving teams a head start on remediation. Among the core capabilities that make a difference are:
-
Automatic Alerts & EscalationA single out-of-spec reading pings on-site staff; unresolved issues escalate automatically to managers as workflow tasks - before they can snowball into downtime or recalls.
-
Bluetooth Sensor MonitoringWireless probes stream temperature and humidity in real time, eliminating manual rounds and the blind spots between them.
-
Verified Task CompletionDigital checklists time-stamp every action and prompt photo proof, ending "pencil-whipped" signatures and giving supervisors iron-clad confidence that the job was done - and done right.
-
Faster Detection, Clearer WorkflowsDeviations surface instantly, with the platform routing ownership so that the right person acts without email chains or guesswork.
-
Less Paperwork, More Problem-SolvingAuto-filled logs and one-click exports slash record-keeping time, freeing teams to address the issues the data exposes - not to chase binders.
-
Automated Summary ReportsTrend dashboards roll up thousands of records into clear visuals, revealing recurring issues a manual review would miss entirely.
Together, these features create a high-resolution, always-on view of operations that no paper checklist could ever match - setting people up to act faster and more confidently.
Technology alone can't close the food safety loop. Humans translate data into effective action and ensure that the digital picture matches reality on the floor.
-
Critical-Thinking Sense CheckOperators still validate an out-of-range alert before a costly product hold or disposal.
-
Guided Root Cause AnalysisSoftware can hold and skim through years of history in seconds, but it's people who decide where to look - framing hypotheses, checking adjacent processes, and testing fixes until the real culprit is confirmed.
-
Context-Rich Hand-OffsWorkflow automation assigns the next task and due time; teammates add the "why" (e.g. "compressor iced after sanitation again") so everyone understands the bigger picture.
-
Leadership & CultureSupervisors model data-driven choices, recognize near-miss reports, and convert dashboard insights into actionable priorities the whole team can rally around.
-
Ongoing Soft-Skill TrainingCoaching, problem-solving, and cross-functional collaboration ensure staff are ready to act on whatever the data reveals next.
When tech and talent are aligned, each alert drives swift, thoughtful action - not confusion or complacency.
-
Role-Based WorkflowsConfigure every alert to generate a task routed to a named role, with automatic escalation if it isn't closed on time.
-
Prompted Verification & CAPA ClosureThe platform schedules device checks and corrective action follow-ups; humans perform the verification and sign off in-app.
-
Blended Training
Combine self-paced e-learning on software basics with live drills (e.g., "Chiller hits +10° on night shift - now what?") to cement skills and muscle memory.
-
Reports Fuel Recurring MeetingsAuto-generated trend reports drop straight into weekly food safety huddles and leadership reviews, turning data into a standing agenda item rather than an afterthought.
-
Streamlined Procedure UpdatesPost-meeting, new SOP templates can be easily published in the system - version-controlled and instantly available - closing the loop from insight → action → new standard.
This cadence embeds continuous improvement into everyday routines, ensuring lessons learned become standard practice instead of forgotten war stories.
Digital monitoring supplies faster detection, instant escalation, and clear ownership; human expertise supplies the judgment that prevents blindspots. Together, they cut paperwork, shrink audit prep, and unlock the time and clarity needed for continuous improvement.
If you're ready to see how tech + talent can look in practice, book a demo with Provision and see how all-in-one documentation management, role-based workflows, and automated reporting can work end-to-end; so your team can spend less time wrestling with records and more time strengthening food safety.