Founded in the Yakima Valley of Washington state over 120 years ago, Congdon Orchards consists of approximately 1,200 acres of pears, apples, and cherries across several growing districts. Their operations also include a packhouse with wet and dry lines that handle not only their own harvests but third-party produce as well.
Sector
Tree Fruit
Headquarters
Yakima, WA
Certifications
SQF
Orchard Size
1,200+ acres
At Congdon, their vertical integration between orchard and packhouse gives them the unique advantage of overseeing a large part of their product from seed to shipment - but the complexities of procedures in their packhouse were difficult to manage on paper. With both a dry and wet packing line to manage, there were multiple sets of sanitation records that needed to be completed, verified, and organized by several shifts on any given day. Human error was becoming a concern, from incomplete fields to indecipherable handwriting - and then Omar Alegria and his team decided to take things digital in order to capitalize on real-time guidance, trend reports, and faster issue detection.
Task Assignment & Follow-Up
-
Operators have clear assignments for specific sanitation tasks, and managers are automatically organized with notifications in multi-step verification workflows
-
Overdue tasks are automatically brought to managers' attention when they've passed their assigned due date
Clean Submissions
-
Incomplete records are caught before submission, and the ability to add comments and pictures gives managers context
-
In-app translation eliminates ESL communication challenges
-
Quick dropdown menus eliminate messy handwriting as an obstacle
Live Deviation Results
-
RLU swab results flag and escalate non-compliant ATP readings
-
CAPA and retests are automatically organized in-line
Trend Insight
-
Configure automatic reports that summarize inspections, swabs, and more
-
Easily sort results to find deviant or near-miss results that require attention
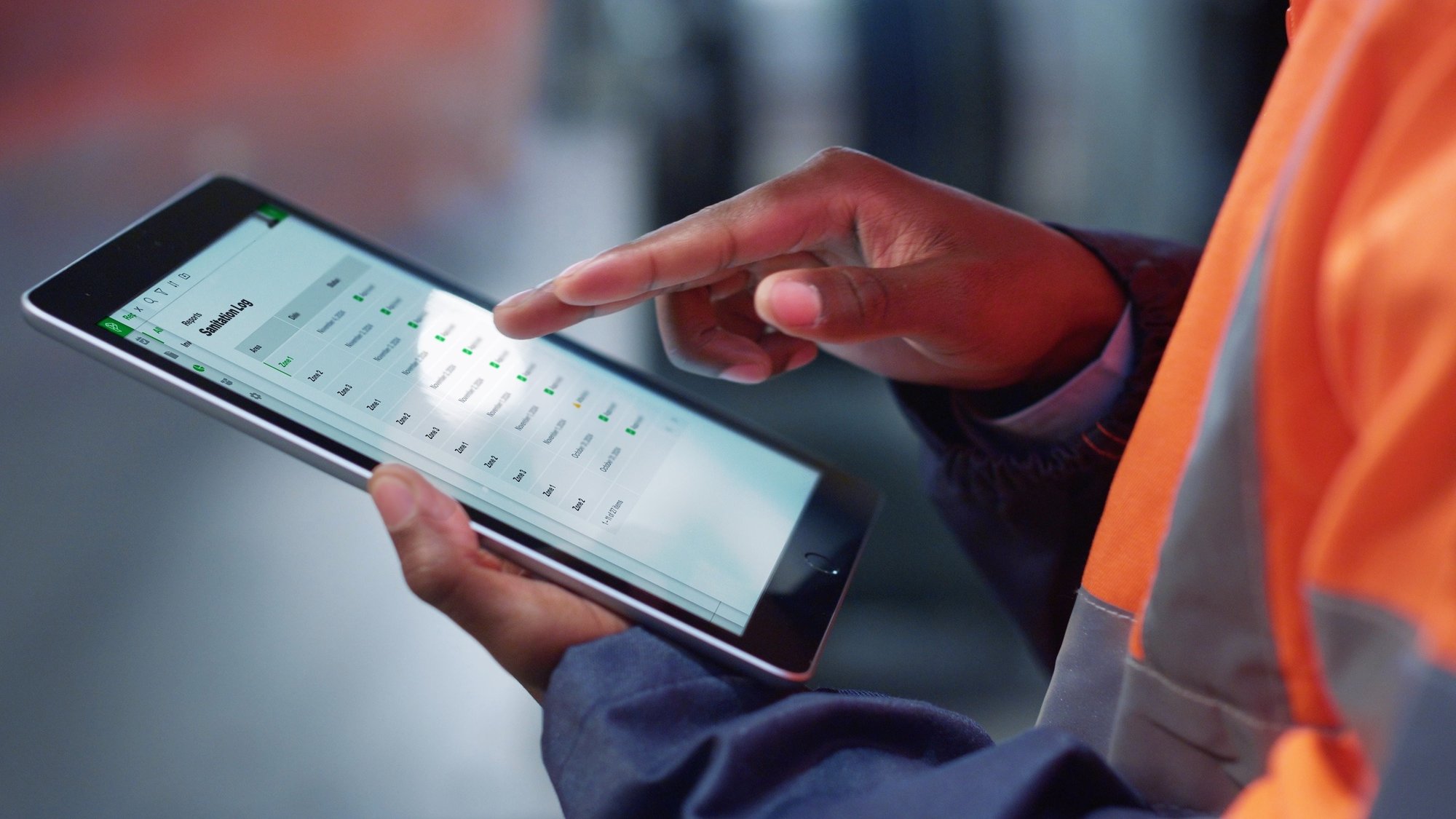
Building on Success
With the implementation of digital documentation through Provision, Congdon's sanitation program is running more smoothly than ever. And even beyond that department, smart tools and automated workflows are helping food safety team members across the operation stay on top of documentation where they struggled with paper before.