The FDA's intention to delay the compliance deadline for FSMA 204 compliance by 30 months offers food safety professionals and companies an extended timeline to prepare and implement robust traceability systems. With the new compliance deadline expected in the summer of 2028, businesses can use this extra time to strategically plan and execute their projects while minimizing risks.
The FDA intends to extend the compliance date for FSMA 204 by 30 months, moving the deadline from January 2026 into summer 2028. This delay was implemented due to recognized challenges in coordinating across complex supply chains, providing food safety professionals and companies more time to prepare and implement effective traceability systems.
Rather than pausing efforts, food safety professionals should treat this delay as a strategic window to optimize compliance plans and enhance operational resilience. With the slow pace of implementation by the industry under the previous deadline, it's clear that looking beyond individual operations and coordinating supplier networks will take a significant time investment and continuous progress. Making the most of the deadline extension is the perfect chance for industry leaders to head up true advancement in food safety and traceability.
To maximize the benefits of this extended timeline, consider the following recommendations:
-
Automate Data Entry
Automation in CTEs is critical to reduce manual entry errors and ensure data accuracy, while enabling operating efficiency.
Example: Build a reference library of recipes to automate ongoing calculations for ingredient quantities during transformation. -
Harmonize Supply Chains
Engage suppliers and customers early and often to prepare a scalable plan for data integration, assessing both the technical methods for data sharing and the standards to unify data references.
Example: Establish whether shipping data is shared via EDI 856 ASN, EPCIS 2.0 API - or both.
-
Conduct Thorough Testing
Identify issues and refine solutions by allowing sufficient time for testing; this should entail both pilot implementations with limited scope, and staging the full-scope implementation in successive phases.
-
Invest in Training and Change Management
Provide comprehensive training and support to employees to ensure they are comfortable with new systems and workflows.
Example: A central library has dubbed screen recordings of key interactions, how-to articles for both hardware and software, a recorded training webinar, a schedule for upcoming live training seminars, and a support contact for instant messaging.
While the specific pace and execution of developing a successful FSMA 204-compliant traceability program will look different for companies of differing sizes, scopes, and commodity types, consider this as a sample action plan created with a multi-product company with approximately 10-50 operating locations.
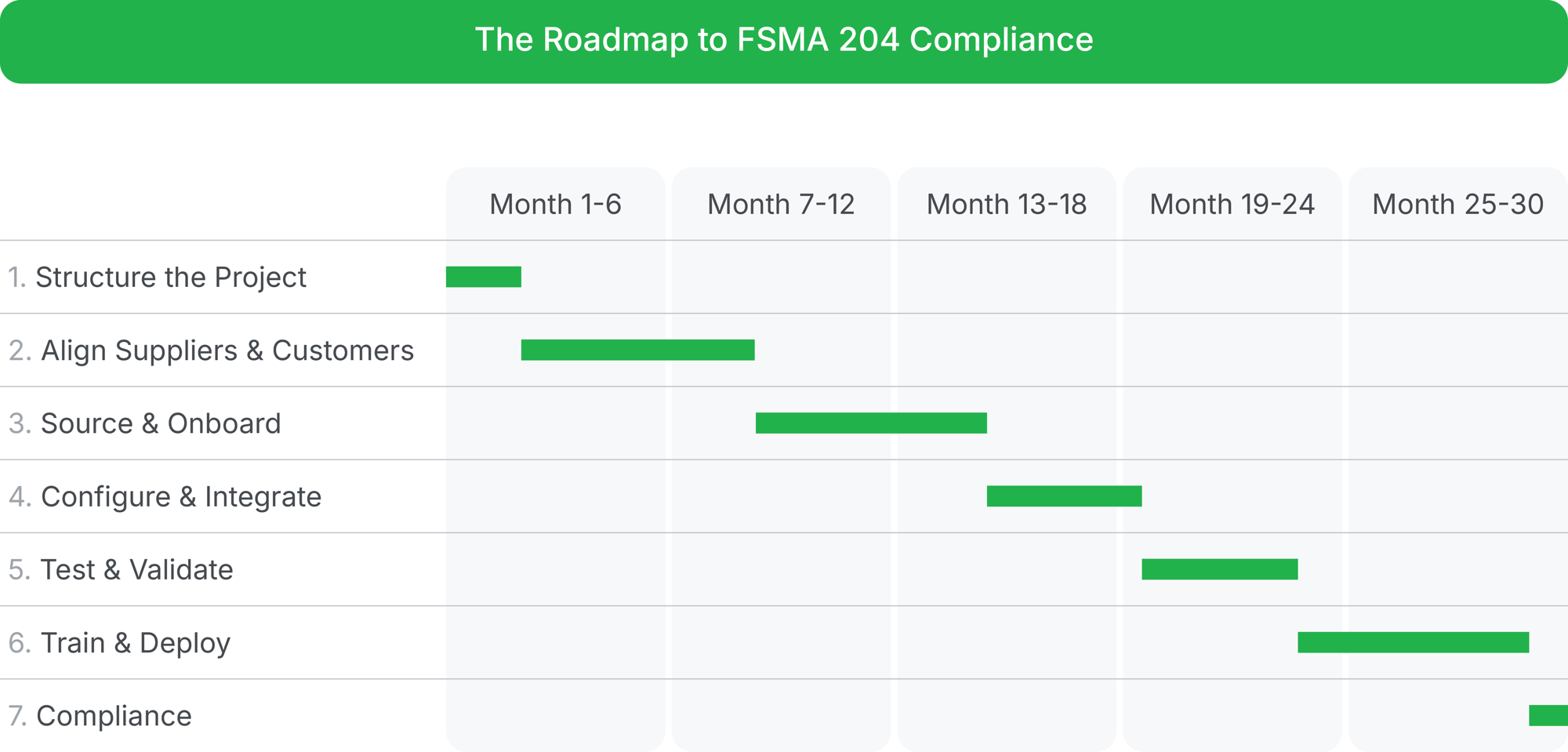
Months 1-2: Structure the Project
Companies must align key stakeholders form various departments to foster collaboration and clarify internal ownership of specific procurement phases. The goal of this phase is to clearly define the scope of the traceability project, preparing requirements for sourcing to enable clear communications with solution providers. Establishing a comprehensive roadmap is crucial to guide the project and keep it on track.
Steps:
-
Assign leads across key internal functions, such as IT, site operations, and regulatory compliance.
-
Investigate and establish the capabilities and limits of current software solutions, hardware, and IT infrastructure.
-
Proactively summarize the count of operating locations, products, and suppliers.
-
Estimate additional elements that may impact software scope, such as the count of users and the count of daily shipments.
Outcome:
A well-defined project structure with clear roles and responsibilities to guide the procurement and implementation process.
Months 2-8: Align Suppliers & Customers
Internal compliance with FSMA 204 is not feasible unless suppliers are first prepared for data transfer. Among the greatest challenges of traceability is enabling interoperable systems, with harmonized data standards. Companies must thoroughly understand best practices and communicate clear expectations both up- and down-stream in the supply chain. Any changes must be accommodated with ample time for suppliers to adapt to new standards. This extended phase is dedicated to developing a comprehensive plan for data integration, ensuring that internal processes are aligned with an entire network of operations.
Steps:
-
Study industry best-practices for data integration - both the means by which data is shared between platforms, and the structure by which data itself is harmonized.
-
Meet with customers and document their requirements for data integration.
-
Draft internal policies for labeling requirements and digital communications.
-
Allow ample time to review policies with key suppliers and harmonize approaches with other industry players.
-
Collaborate with IT stakeholders to plan integrations, such as EDI 856 or EPCIS 2.0 API data sharing for Advanced Shipping Notices.
-
Prepare and send detailed communications outlining supplier requirements for data sharing.
-
Allow suppliers sufficient time - often 6 to 12 months - to achieve compliance with policies.
Outcome:
A clear integration plan that aligns suppliers to meet your traceability requirements as well as those of your customers, reducing risks of missing data during implementation.
Months 9-14: Source & Onboard
Selecting the right software solution is more challenging - and more critical - than it may appear. To ensure a strong long-term fit, food companies should dedicate ample time early on to assess their operational and technical needs. It's important to consider detailed, day-to-day requirements of users and facilities, as well as the integration requirements to sync with existing hardware and software. This preparation helps avoid tools with flashy features but low fit. In many cases, a software evaluation process spans several months, involving deep dives across many departments before selecting a solution that will truly support FSMA 204 compliance.
Steps for companies with existing software:
-
Audit current systems to identify gaps in CTE and KDE capture.
-
Shadow real-life workflows to document facility and user requirements.
-
Study hardware and IT infrastructure to document technical requirements.
-
Assess developer documentation to gauge interoperability.
-
Determine extensibility of the software configuration to address requirements.
Steps for companies needing new software:
-
Shadow real-life workflows to document facility and user requirements.
-
Document technical requirements based on hardware and IT infrastructure.
-
Have compliance stakeholders lead discovery and review traceability demos, advancing in several meetings from general to custom-configured.
-
Add IT stakeholders to review technical specifications for configuration and integration.
-
Add project stakeholders to review implementation plans and support methods.
-
Allow time for formal budget and legal reviews with leadership.
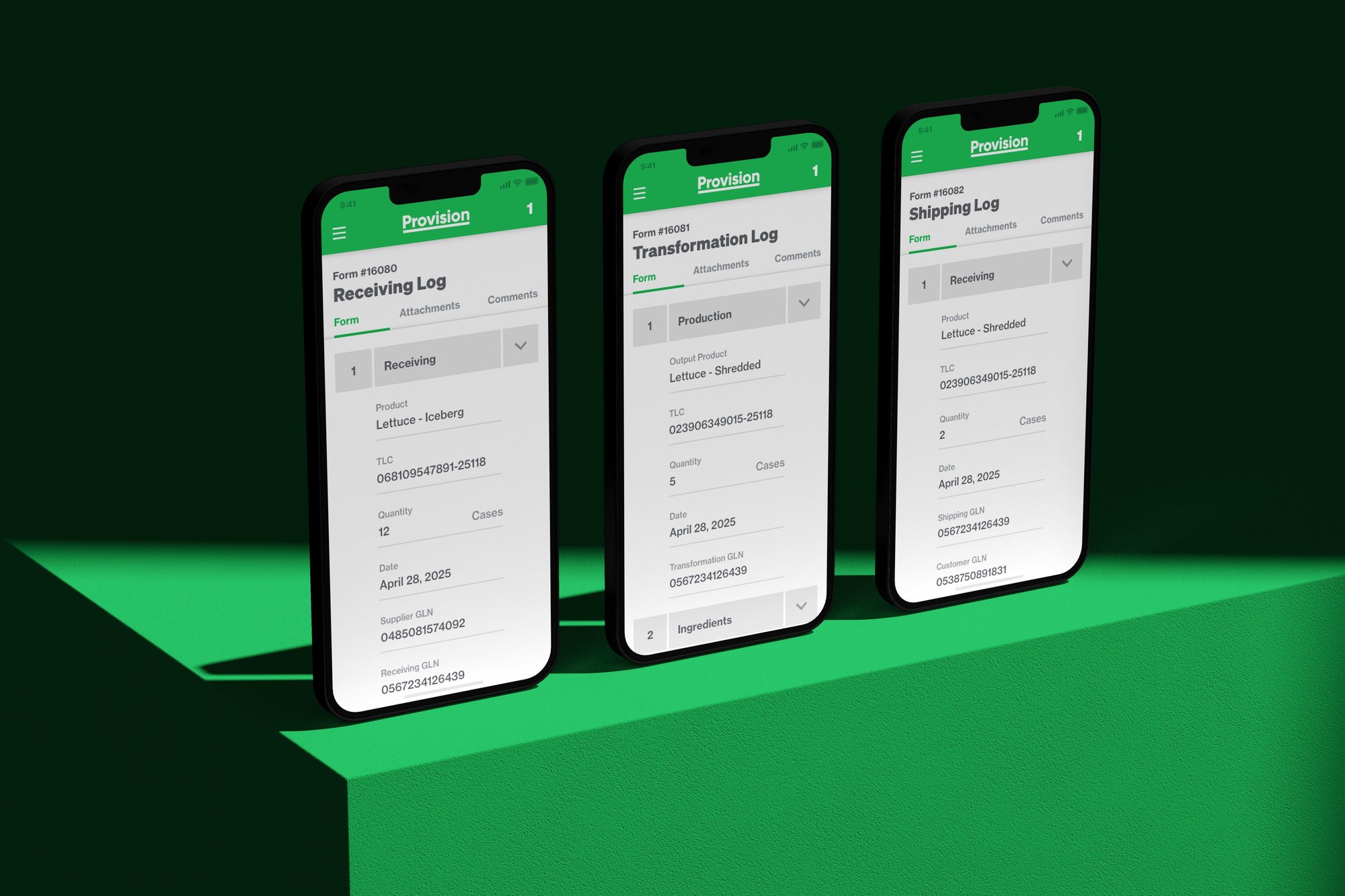
Months 15-18: Configure & Integrate
The focus shifts to the practical implementation of internal record-keeping, reporting and system integration. This involves developing and testing integrations between internal systems and supplier platforms to ensure seamless data flow. To ensure adoption among non-technical operators who must capture data, it's critical to configure, test, and validate CTE record templates, assessing how they fit with operating workflows, and how to best support ongoing compliance.
Steps:
-
Align record-keeping plans by defining where and how CTEs will be recorded.
-
Prepare IT infrastructure by procuring hardware, preparing WiFi, and more.
-
Document configuration specs by studying requirements such as operator languages, device limitations, and internet persistency.
-
Structure and upload common KDE references, such as supplier lists, product recipes, and operating addresses.
-
Prepare compliance guard rails such as task alerts, standard operating procedures, and location compliance dashboards.
-
Configure reports that will summarize ongoing record submissions.
-
Facilitate supplier onboarding for data transfer.
-
Write API integrations or prepare EDI communications as needed.
Outcome:
Operational systems are configured for seamless traceability record-keeping across all steps in the supply chain.
Months 19-22: Test & Validate
Before full deployment, it's essential to rigorously test the system to identify and address any potential issues. This involves validating system configurations through pilot testing at select sites and refining processes based on the test results. Companies should prepare for deployment by developing a comprehensive change management plan.
Steps:
-
Identify testing locations, confirm availability and timelines, and prepare their stakeholders.
-
Test the integrations that were developed to ingest data from third-parties and between internal systems.
-
Test record-keeping inside live operations to inform iterative improvements to the software configuration.
Outcome:
Systems are validated and ready for deployment across all operating locations.
Months 23-29: Train & Deploy
With all systems validated, the focus turns to rolling out traceability across all operating locations in a structured manner. This first involves the development of training resources for employees to ensure they are competent and capable of adopting new systems and processes. Management teams should proactively initiate internal processes for issue escalation and support to ensure readiness for ongoing compliance. This step could take as little as one month, or stretch far beyond the timeframe suggested, up to a year.
Steps:
-
Develop training resources, considering a mix of on-site and remote, live and asynchronous assets, which may include articles, videos, posters, webinars, in-person seminars, and more.
-
Plan implementation stages across all operating locations in staged waves of adoption - not all at once.
-
Develop and communicate a change management across levels of the organization.
-
Initiate internal support processes to address any issue during rollout phases.
-
Support the rollout process with continued employee communication.
Outcome:
Operating staff are trained and systems supporting FSMA compliance are actively used across all operational sites, supported by ongoing strategies for communication and support.
Months 30+: Operate
The final phase focuses on maintaining the implemented traceability system and ensuring its long-term effectiveness. This involves establishing internal ownership of FSMA 204 workflows, onboarding new suppliers and products, and periodically reviewing processes to identify and address any gaps or inefficiencies.
Steps:
-
Maintain internal ownership of FSMA 204 workflows by assigning dedicated teams or roles for oversight.
-
Onboard new suppliers, products, or sites into your traceability program as your business grows or changes.
-
Periodically review processes and address compliance or data quality gaps.
Outcome:
A resilient traceability program capable of adapting to business growth while maintaining regulatory compliance.
Conclusion
The FDA's delay in FSMA 204 compliance offers food companies a strategic opportunity to thoroughly prepare and implement robust traceability systems. By following the timeline-based approach outlined above, businesses can not only meet regulatory requirements but also enhance operational efficiency, improve supply chain visibility, and strengthen consumer trust. Taking proactive steps now will enable companies to turn compliance into a competitive advantage while safeguarding public health.