Process
Grower, packer, shipper
Headquarters
Commerce, CA
Certifications
SQF
Facility Size
160,000 square feet

Lydia Ortega and the team at 4Earth Farms weren't strangers to the challenge of managing the sampling and testing program at the company's large primary facility. Collecting, verifying, and organizing the piles of paperwork filled out multiple times per day for the huge range of seasonal products was overly-complex and prone to human error - it was time for a change.
Pre-programmed Sampling Rotations Ensure Coverage
-
Built-in rotations eliminate guesswork or errors in selecting sites to sample
-
Sampling sites in rotations can be further subdivided by zone to ensure thorough testing of all vulnerable areas
-
Customizable workflows give managers additional flexibility to add new zones or sampling locations as needed for spot-checks or follow-up
Automation Allows for Faster, More Accurate Identification of Issues
-
Automatic time stamps allow for accurate tracking of failed tests and association of at-risk product with out-of-spec results
-
Built-in pass/fail notifications clearly indicate to operators and management when results are out of spec
-
Quick dropdown menus eliminate messy handwriting as an obstacle
Comprehensive Workflows Streamline Retesting Procedures
-
Failing test results can be quickly and easily pushed into a retest workflow and immediately sent to the relevant operator(s) for completion
-
Workflow steps are captured in an auditable, time-stamped history that can prove collaboration and food safety culture
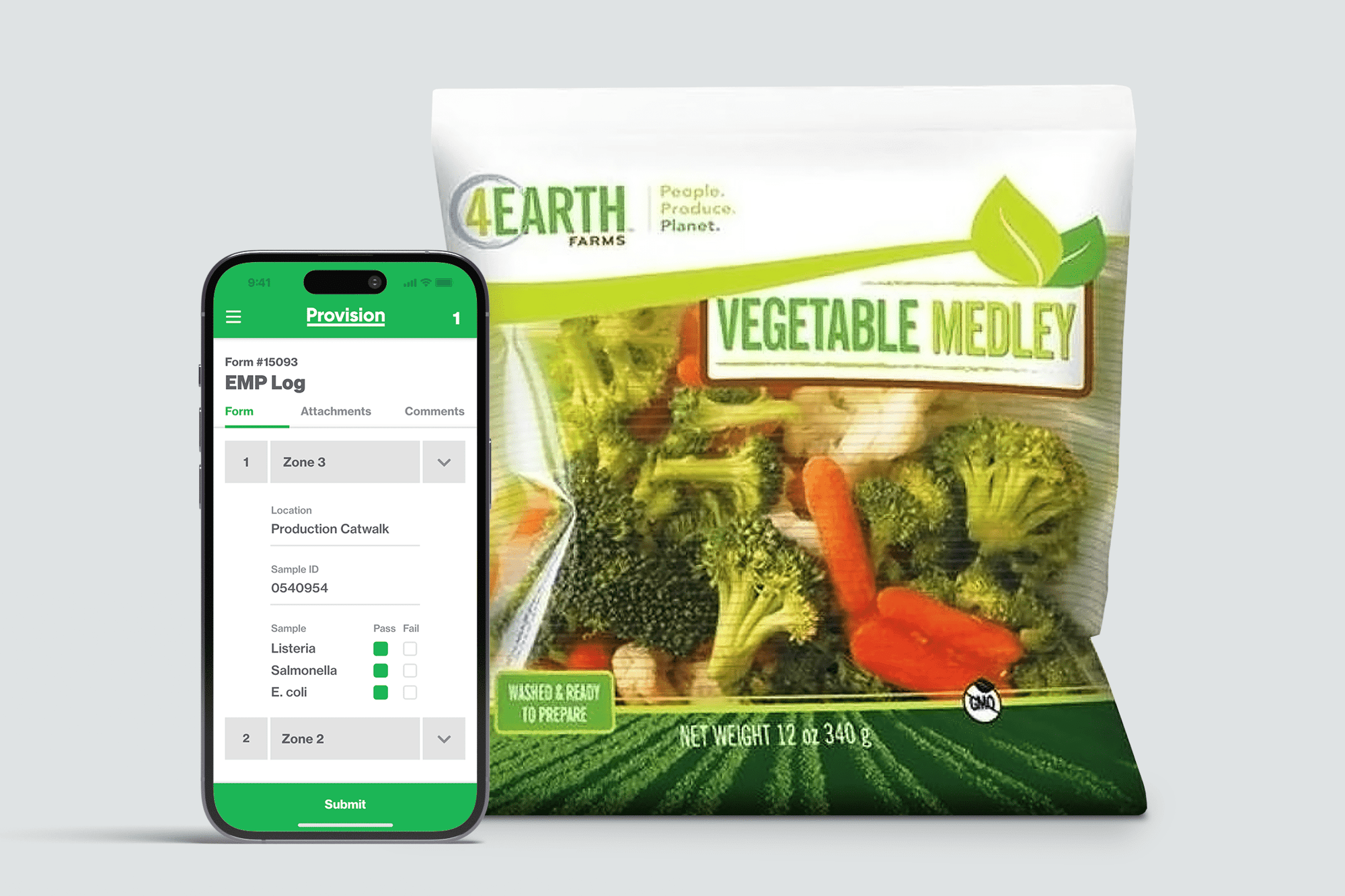
Building on Success
By eliminating the risk of human error through the application of Provision's smart tools, automation, and intuitive design, Lydia and the 4Earth team are looking forward to a smoother, more streamlined experience with their sampling and testing procedures. As the business continues to grow, Provision's platform has also been incorporated into other aspects of the food safety management system, ensuring a holistic approach that will see them well into the future of the business.