Mid-market grocers face significant challenges in meeting FSMA 204 traceability requirements without disrupting daily operations, but by focusing on automation, data standardization, and system unification, they can achieve compliance efficiently and effectively.
Accurate data entry at the receiving stage is the foundation of FSMA compliance. Time studies show that manual data logging can take up to 21 hours per day in a single grocery location - an unsustainable burden that may lead to rushed, non-compliant data. The solution? Automation
-
Advance Shipping Notices (ASNs)Ingest data from suppliers to automatically pre-fill 7 of 8 Key Data Element (KDE) types during receiving.
-
GS1-128 Barcode ScanningExpedites the capture of KDEs such as supplier and product information, and is particularly useful when ASNs aren't available.
-
Structured Data LibrariesBefore receiving begins, prepare common data references such as addresses, phone numbers, and other KDEs that can autofill receiving logs.
By automating data capture for inbound loads, grocers ensure a strong foundation for accurate and efficient traceability.
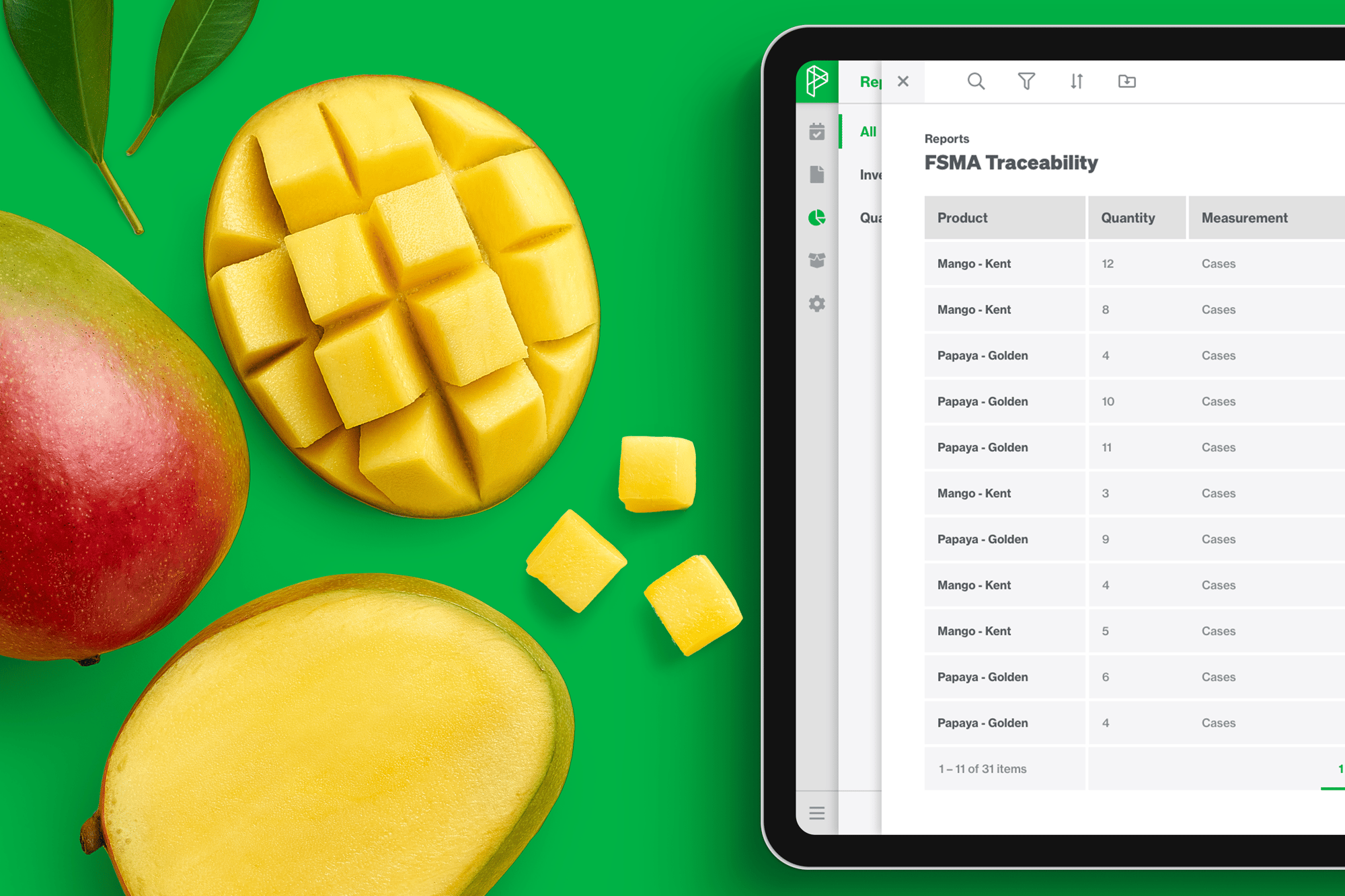
Transformation records are critical in deli, bakery, and commissary operations, where it's common for goods to be transferred between grocery locations. Time studies reveal that manual logging can take 11 minutes per finished good, causing a single store to require two full time employees for record-keeping alone. However, digital record automation can eliminate more than 80% of this time.
-
Data TransferBy harmonizing production systems with logistics systems, KDEs from the receiving stage can seamlessly transfer into the transformation stage, vastly reducing data entry requirements.
-
Inventory TrackingMany stores track inventory only at a store level. By instead tracking inventory specific to the transformation operation, operators will have an easier time selecting the ingredient lots available to fulfill recipes.
-
Recipe AutomationSignificant time can be eliminated in transformation by looking up to centrally-managed recipe sheets, automating calculations and preventing mathematical errors for the quantities of ingredients used.
By reducing manual inputs, grocers can minimize errors and ensure a reliable transformation process.
While record contents may be autofilled, they could still be missed or misunderstood by high-turnover staff who are new to traceability requirements. To ensure data integrity, management must prepare automated guardrails that require low-to-no supervision.
-
Task AssignmentsTo prevent missed records, connect traceability events in a workflow, such that records like Advanced shipping Notices can prompt subsequent records from the operator, such as a Receiving Log.
-
Live TranslationTo support a diverse workforce in reading and writing data for Critical Tracking Events (CTEs), plug into tools such as Google Translate and enable real-time support for up to 109 languages.
-
Embedded GuidanceAssume that operators will forget portions of their traceability training, and enable continuous reinforcement by displaying related work instructions and image-driven SOPs inside related CTE records.
With scalable safeguards in traceability records, off-site managers can protect their ability to have accurate, complete, and compliant data for traceback.
The scope of traceability records grows exponentially with each incremental event in the supply chain. If a grocer faces a recall of a single supplier product, they may easily trace 12,000 records - an overwhelming task without a centralized system. The key to compliance is data unification.
-
One Central Data HubThe safest solution for traceability is to capture and report on data within a single system, which limits the risk of broken integrations.
-
Integrated SystemsWhen it's necessary to use multiple systems to complete traceability records, they must be unified into a central reporting hub to prevent exponentially duplicated traceability searches in the event of a recall or outbreak.
-
Intuitive ExportIf IT is required to access, patch, and export data, submission deadlines may cause strain; ensure that any head office compliance manager has access to trace and export sortable spreadsheets with intuitive and direct controls.
A centralized system simplifies traceability, making it easier to meet the FDA's 24-hour recall submission deadline and maintain compliance.
Mid-market grocers don't have the luxury of adding extra staff just to meet FSMA 204 requirements. Instead, the key to compliance lies in automation, data standardization, and system unification - keeping operations running smoothly while ensuring full regulatory adherence.